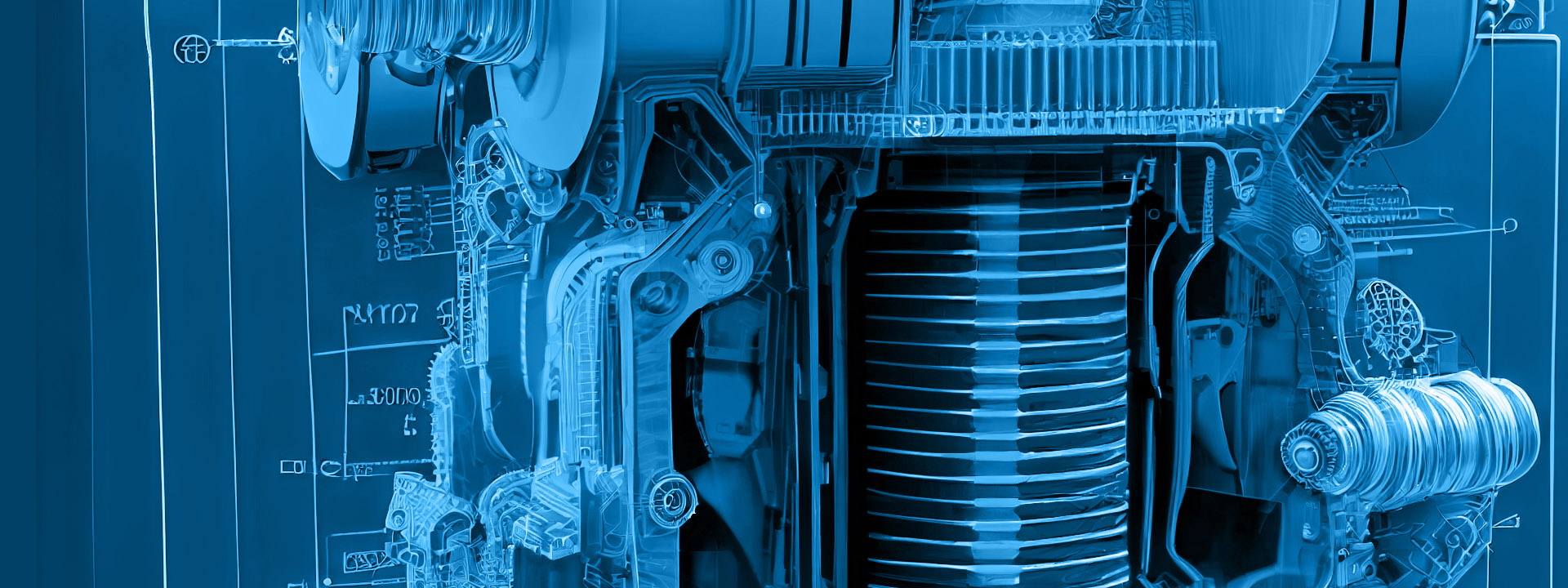
Screw/Nut system
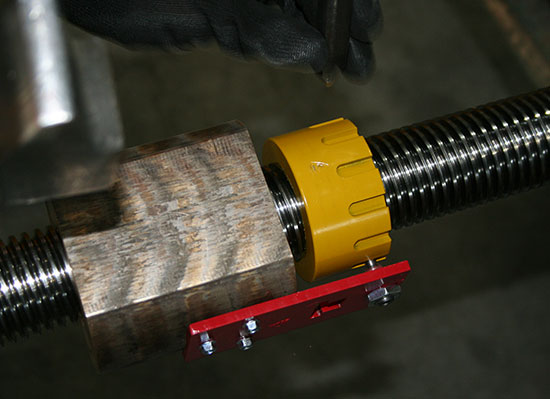
SEFAC screw/nut system vs hydraulic systems
There are many advantages of the SEFAC screw/nut system over hydraulic systems
The SEFAC screw/nut principle is inherently irreversible as the angle of inclination of the screw pitch does not allow the fork to go down without the operation of the motor gearbox. This prevents the carriage supporting the vehicle from moving without operator intervention.
In addition, we guarantee the safety of our equipment by systematically testing each column on our test bench before it is released. During these tests, the columns are subjected to loads up to 50% higher than their rated Safe Working Loads.
As hydraulic technology is not naturally safe, a safety system (ratchet) must be added. In order to work safely, this ratchet abuts against a notch every 5 cm or so, which limits your true-lock positioning options.
With SEFAC columns, you can precisely choose your lifting height
The long rachet mast on hydraulic columns raise with the vehicle often blocking access to the cab doors but also passing very close to the vehicle’s windows and coachwork causing the increased potential to damage these, especially in the event of under-inflated or damaged tyres or defective suspension.
SEFAC column lifts will not buckle as the screw is suspended
The forces are therefore exerted vertically on the screw and not laterally.
In hydraulic systems, the cylinder is stressed at the top and bottom and applies a force from the bottom to the top while the load applies a force from the top to the bottom. As a result there is a risk of buckling at the slightest wear of the plates and guide joints, leading to premature wear of the cylinders.
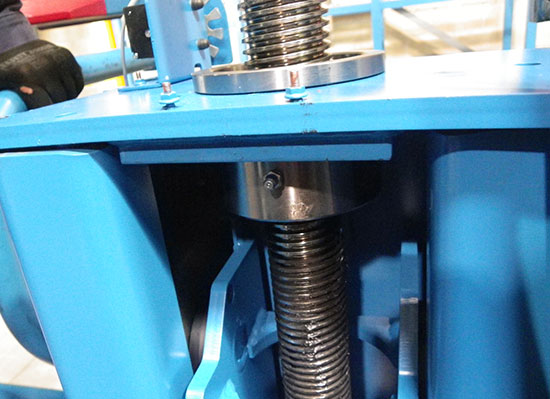
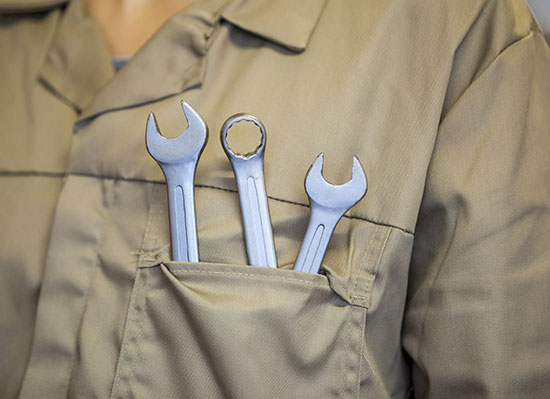
Simplified design = simplified maintenance
Thanks to the mechanical technology, the design is simpler, requiring fewer components and therefore less maintenance:
- On SEFAC’s screw & bronze nut mobile columns, you only have to grease the nut regularly (manually or with automatic greasers to be replaced every year). This support nut must be changed on average every 5,000 cycles (i.e. every 10 years at a rate of 2 cycles per day) and this operation only requires 15-30 minutes for disassembly and reassembly.
The suspension stop of the screw must be greased once a year;
On the ball screw model, there is even less mechanical maintenance: the suspension stop of the screw must still be greased once a year, however, the support nut only needs to be greased every 5 years.
Conversely, hydraulic columns require more regular maintenance as the seals allow the hydraulic oil to escape and allow air intake.
Therefore, you will need to:
- Regularly purge/bleed the system (1 or 2 times per year);
- Change the oil in the 4 drums every 1 to 2 years;
- Grease the wiper seals regularly;
- Check that there are no signs of impact on the cylinder rod: with the slightest impact or scratch on the cylinder, it must be changed because the sealing is no longer guaranteed;
- Regularly replace the seals and guide plates to avoid buckling (bending) of the cylinder.